Aujourd’hui, de nombreuses entreprises envisagent la réindustrialisation. Permettant de mieux maîtriser la production, les délais mais aussi les coûts, cette stratégie a toutefois de nombreuses conséquences pour la supply chain. Et différents facteurs sont à prendre en compte pour que cette réindustrialisation soit synonyme de réussite… Décryptage.
Rapatriement des activités de production : état des lieux
Au cours des années 2000, de nombreuses entreprises ont fait le choix, principalement pour des raisons de coût, de transférer leur production à des fournisseurs étrangers. Mais les différentes crises liées au Covid, à la guerre en Ukraine et à l’inflation ont changé la donne.
Les industriels ont pris conscience que faire fabriquer ses produits à des milliers de kilomètres pouvait poser toutes sortes de problèmes tant du point de vue de la qualité, de la sécurité que de la planification et de la gestion des priorités.
Certaines problématiques de fond prennent également de l’importance dans la stratégie des entreprises. L’impact écologique, les modes de production éthiques et les émissions de carbone sont désormais au cœur des préoccupations.
Dans ce contexte, de plus en plus de sociétés décident finalement de réindustrialiser, c’est à dire de rapatrier leur production en France ou près de nos frontières.
Ainsi, actuellement, environ 80% des produits de grande distribution sont issus d’une industrie qui a été relocalisée. De même dans l’automobile, des usines d’assemblage reviennent en France, alors qu’elles étaient encore il y a peu, implantées en Chine.
Pourquoi les entreprises réindustrialisent-elles ?
Après plusieurs décennies de délocalisations, les industries ne considèrent plus que le futur est de disposer de toujours plus d’usines à travers le monde et de sous-traiter. Elles semblent désormais faire machine arrière. Plusieurs raisons expliquent ce choix :
La maîtrise du risque
L’un des enjeux majeurs de la relocalisation est de réduire l’exposition de l’entreprise aux risques. Notamment, au risque de rupture d’approvisionnement et de pénurie. La crise en Ukraine a par exemple fait prendre conscience que la France était très dépendante de ce pays pour l’huile de colza, l’huile de tournesol, la moutarde et les céréales. Ce qui a engendré des situations de rupture, notamment dans les grandes surfaces… Relocaliser la production permet de réduire ce risque.
Le savoir-faire et la qualité
Relocaliser, c’est garder la main sur son savoir-faire. Un point crucial, au cœur des valeurs de l’entreprise. En relocalisant, l’entreprise limite considérablement les problèmes de non-qualité. De plus, elle court beaucoup moins de risques de se faire copier ses produits originaux !
La maîtrise des délais
La délocalisation implique des délais de livraison longs et mal maitrisés. La relocalisation réduit ces délais et permet à l’entreprise de gagner en agilité, tout en évitant les risques de ruptures de stock.
La réduction des coûts
Contrairement aux idées reçues, délocaliser n’est plus forcément synonyme de réduction des coûts. En effet, le coût du transport depuis la Chine ayant tout de même été multiplié par dix ces trois dernières années, la fabrication hors des frontières européennes a perdu en attractivité.
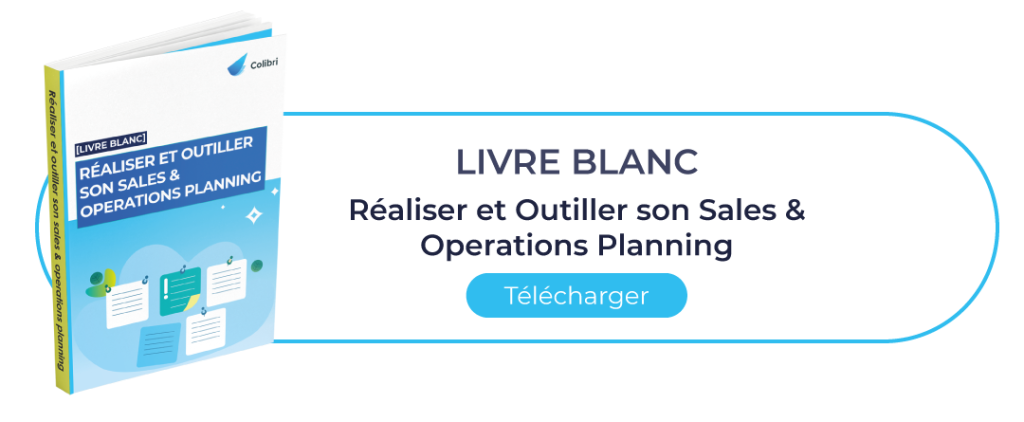
Réindustrialisation : des exemples inspirants
Des entreprises font donc le choix de faire marche-arrière. Parmi elles : Smoby dont les usines de production ont été réimplantées en France. Le numéro 1 français du jouet a ainsi créé en 2022 pas moins de 95 emplois à Arinthod, dans le Jura.
Autre exemple de relocalisation réussie, celle de Kusmi Tea. Face à une augmentation des coûts et au manque de réactivité des sites de production éloignés, l’entreprise a choisi de relocaliser la fabrication de ses boites en métal et l’ensachage du thé du Maroc et de la Chine vers la France.
À noter : l’État soutient aujourd’hui la relocalisation dans le cadre du plan FranceRelance. Un programme national qui comporte des mesures de soutien aux entreprises et aux salariés. Un volet est spécifiquement dédié au soutien à la relocalisation industrielle, notamment dans des secteurs critiques tels que la santé, l’agroalimentaire, l’électronique, les intrants essentiels de l’industrie et la 5G.
Rapatriement des activités de production : quels enjeux et conséquences pour la supply chain ?
Il y a aujourd’hui beaucoup d’exemples encourageants de relocalisations réussies. Cependant, il faut garder à l’esprit qu’une relocalisation est toujours synonyme de changements majeurs pour l’entreprise. Avec l’arrivée – ou le retour – du volet production, certaines entreprises vont devoir repartir quasiment de zéro !
Les entreprises qui relocalisent doivent passer par une phase d’adaptation, où le fonctionnement global est totalement remis en question. Progressive, cette phase plus ou moins longue passe par différentes incertitudes, tâtonnements, notamment à propos des capacités de production. Durant cette phase transitoire, l’entreprise reprend la main sur la production et réalise en parallèle des approvisionnements complémentaires pour les produits qu’elle n’est pas encore en mesure de fabriquer.
La supply chain doit par ailleurs se réadapter à des délais et des tailles de lots radicalement différents. Plus besoin désormais de disposer de plusieurs mois de stocks d’avance alors que l’usine relocalisée peut produire en seulement 15 jours, par exemple.
En définitive, la réindustrialisation doit nécessairement passer par la conduite de changement. Ce processus permet notamment de réapprendre à l’entreprise le métier de la production et l’aide à changer des habitudes souvent ancrées depuis de nombreuses années.
La réorganisation en matière de personnes et d’outils autour de la planification industrielle à long terme demande également de tout repenser de A à Z. Or, c’est un point très critique de la supply chain. Pour que la conduite de ce changement soit totalement réussie, certains piliers fondamentaux doivent être respectés. L’un des challenges majeurs consiste à aligner les fonctions de supply chain et de stratégie, de faire monter en compétences certains collaborateurs au moyen de formations adaptées et de recruter pour la fabrication.
Enfin, il est nécessaire de mettre en place un système collaboratif ou chacun communique et où aussi bien les services commerciaux que financiers interviennent pour ajouter leurs connaissances métier à la planification. Dans ce contexte, la meilleure des options consiste à opter rapidement pour un outil S&OP collaboratif et intelligent !
La réindustrialisation est un processus ultra stratégique. Pour faciliter vos démarches, choisissez une solution adaptée à vos contraintes. L’outil Colibri S&OP facilite la transition et met en place un processus S&OP qui vous permet de profiter d’une réelle visibilité, d’accorder tous les acteurs mais aussi, d’aligner le stratégique à l’opérationnel. Colibri S&OP vous accompagne dans le pilotage collaboratif de votre processus de réindustrialisation ! À la clé : des gains en flexibilité et en compétitivité. Pour reprendre la main sur votre supply chain : contactez-nous !
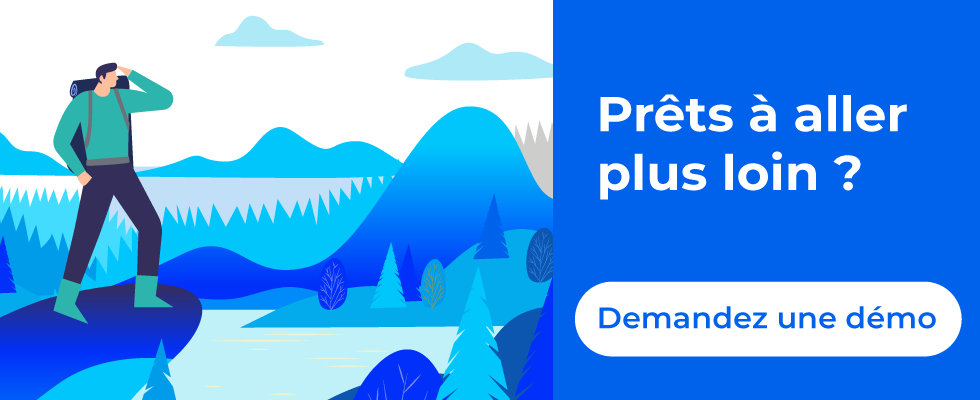